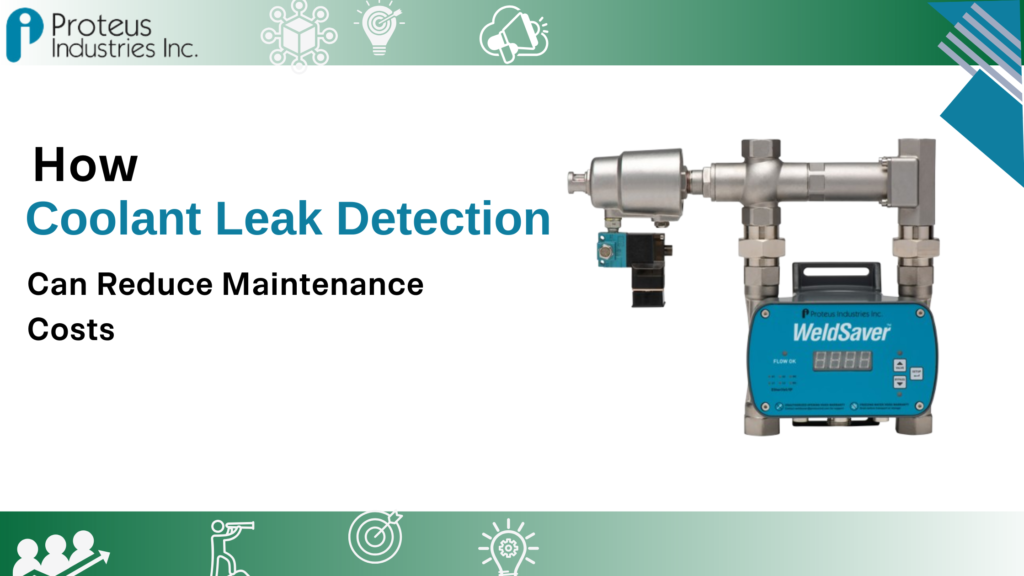
How Coolant Leak Detection Can Reduce Maintenance Costs
Effective coolant leak detection is crucial for industrial operations to prevent unexpected machinery failures and reduce maintenance costs. Industrial equipment heavily relies on cooling systems to maintain optimal performance, and even minor leaks can lead to severe consequences, including overheating, equipment breakdowns, and financial losses. Implementing advanced coolant leak detection solutions can help industries enhance efficiency, minimize downtime, and extend the lifespan of their machinery.
The Importance of Coolant Leak Detection in Industries
Industries that use heavy machinery and cooling systems, such as manufacturing, automotive, and aerospace, require continuous monitoring of coolant levels. A small coolant leak may seem insignificant, but over time, it can:
- Cause overheating in machinery
- This leads to expensive repairs
- Reduce the efficiency of industrial processes
- Increase energy consumption
- Pose safety risks to workers
Industries can mitigate these risks by investing in coolant leak detection and optimizing maintenance schedules.
How Coolant Leaks Increase Maintenance Costs
Coolant leaks can be costly for industries due to several factors:
1. Increased Repair Costs
When coolant leaks remain undetected, they can cause severe damage to machine components such as pumps, engines, and cooling systems. Replacing damaged parts can be expensive, and frequent breakdowns lead to higher maintenance costs.
2. Equipment Downtime
A coolant leak can result in unscheduled downtime, which affects production timelines and reduces operational efficiency. Companies may lose significant revenue due to halted operations while repairs occur.
3. Energy Inefficiency
Leaking coolant reduces the cooling system’s effectiveness, forcing machines to work harder and consume more energy. This inefficiency leads to increased energy costs and reduces the overall performance of the equipment.
4. Safety Hazards
Leaks can cause slippery surfaces, increasing the risk of workplace accidents. In addition, overheating equipment poses fire hazards, endangering employees and assets. Addressing leaks proactively helps maintain a safe working environment.
How Coolant Leak Detection Helps Reduce Maintenance Costs
1. Early Leak Detection Prevents Major Failures
Advanced coolant leak detection systems identify leaks early, allowing industries to address minor issues before they escalate into costly repairs. Early detection helps in:
- Avoiding significant machinery failures
- Reducing the need for emergency repairs
- Extending the life of industrial equipment
2. Scheduled Maintenance Instead of Emergency Repairs
With accurate coolant leak detection, industries can plan maintenance activities efficiently rather than dealing with unexpected breakdowns. This proactive approach helps in:
- Reducing operational disruptions
- Allocating resources effectively
- Ensuring machinery remains in optimal condition
3. Cost Savings on Coolant Refills
A persistent coolant leak leads to frequent coolant refills, increasing operational costs. Detecting and fixing leaks promptly prevents unnecessary coolant wastage, saving industries money in the long run.
4. Enhancing Equipment Efficiency
Efficient cooling systems ensure that machinery operates at peak performance, reducing component strain and overall maintenance expenses. Coolant leak detection helps maintain optimal equipment efficiency by preventing overheating and performance degradation.
Methods of Coolant Leak Detection
Several techniques are used for coolant leak detection, including:
1. Visual Inspection
Regular visual checks of coolant levels, hoses, and connections help detect leaks early. Signs of leaks include visible coolant puddles, damp hoses, and discoloration.
2. Pressure Testing
A pressure test identifies leaks in the cooling system by pressurizing the system and checking for pressure drops. This method is commonly used in industrial maintenance.
3. Thermal Imaging
Infrared thermal imaging detects temperature variations in cooling systems, highlighting potential leak points. This non-invasive method improves leak detection accuracy.
4. Sensor-Based Leak Detection Systems
Industries can use sensor-based systems to monitor coolant levels and detect leaks in real time. These systems provide alerts when coolant levels drop unexpectedly, enabling immediate corrective action.
Why Choose Proteus Industries for Coolant Leak Detection?
At Proteus Industries, we provide high-quality coolant leak detection solutions tailored for industrial applications. Our advanced detection systems offer:
- Real-time monitoring to detect leaks instantly
- Highly accurate sensor technology for precise leak identification
- Customizable solutions to meet industry-specific needs
- Reliable and durable equipment designed for industrial environments
By partnering with Proteus Industries, industries can benefit from reduced maintenance costs, improved operational efficiency, and enhanced equipment longevity.
Conclusion
Investing in coolant leak detection is a cost-effective strategy that helps industries reduce maintenance expenses, prevent costly equipment failures, and ensure smooth operations. By implementing advanced detection technologies and partnering with reliable solutions like those offered by Proteus Industries, businesses can optimize their maintenance practices, enhance energy efficiency, and maximize productivity. Proactive leak detection saves money and contributes to a safer and more sustainable industrial environment.
For more information on our coolant leak detection solutions, visit Proteus Industries.
Leave Your Comment